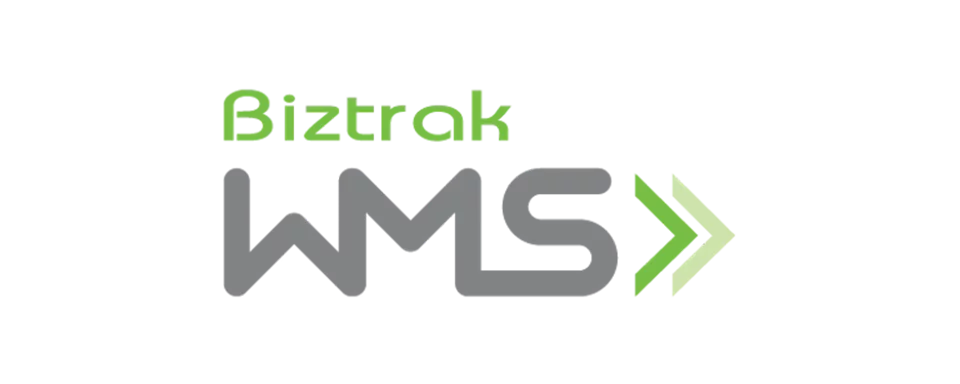
A ROBUST WAREHOUSE MANAGEMENT SYSTEM FOR REAL-TIME OPERATIONS
BIZTRAK WMS is robust and real-time warehouse management system (WMS) that is designed to meet the most dynamic warehouse environment especially 3PL warehouses that are required to fulfill the needs of various different customers. Biztrak WMS is high-functionality yet user-friendly, it streamlines your warehouse operations and provides greater control over inventory movement with real-time update.
We belive as a software that drives the busy warehouse operation, rapid response and user friendliness are the keys to get the job done well. Our services include Warehouse Process Consultancy, Software Customization and Business Reporting Creation.
Why Biztrak WMS
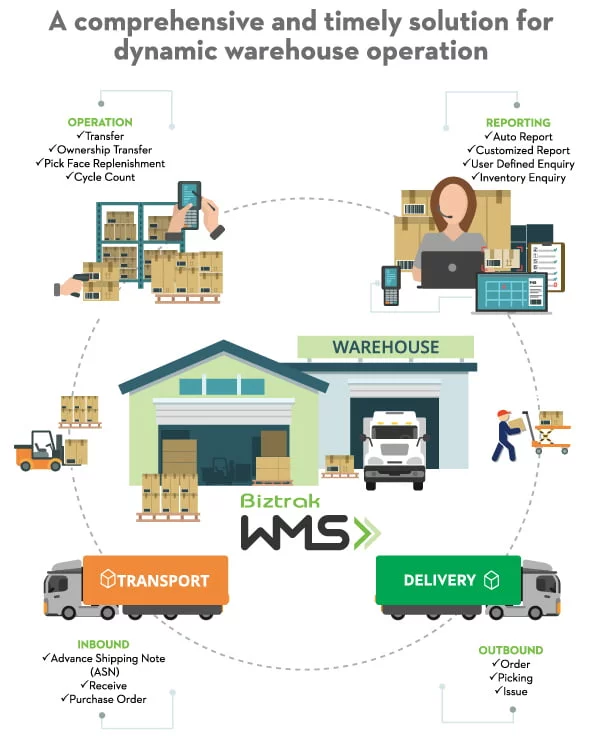
An integrated warehouse inventory management software which is designed to improve
the efficiency, accurancy and operating cost of warehouses.
Modules & Features
Features | Descriptions |
---|---|
Purchase Order |
|
Advance Shipping Notice |
|
Receive |
|
Features | Descriptions |
---|---|
Order |
|
Picking |
|
Combined Picking |
|
Packing |
|
Issue |
|
Issue |
|
Features | Descriptions |
---|---|
Transfer |
|
Ownership Transfer |
|
Pick Face Replenishment |
|
Cycle Count |
|
Bin Put-away Allocation |
|
Features | Descriptions |
---|---|
Biztrak Auto Report |
|
User Customizable Report |
|
User Definable Enquiry |
|
Features | Descriptions |
---|---|
Multi warehouse capability |
|
Flexible Bin Structure |
|
Multiple UOM and Variant |
|
Inventory by multiple parties (Multi Customer) |
|
Picking Algorithm |
|
Customized business document by Party |
|
Auto trigger Product Expiry |
|
Features | Descriptions |
---|---|
User Defined Fields |
|
Security & Access Traceability |
|
Collaboration |
|
Multilingual Support |
|
Import External Data |
|
Export Data |
|
User Definable Transaction Type |
|
State-of-the-art Data Grid |
|
Duplicate Document |
|
Bookmark |
|
Features | Descriptions |
---|---|
Customer Web Portal |
|
Features | Descriptions |
---|---|
Mobile Application |
|
- Order transaction
- DHL Courier Service Provider for the shipment booking and shipping label.
- Citylink Courier Service Provider for the shipment booking and shipping label.
- Daily Issue by Item Categories
- Daily Issue by Item Type
- Daily Receive by Item Type
- Daily Receive by Item Categories
- Physical Inventory by Item Categories
- Current Physical Inventory VS Usable Inventory
- Physical Inventory by Item Types
- Daily ASN Status
- Daily WEB ASN Status
- Daily Order Status
- Daily WEB Order Status
Kitting module is a crucial component in warehouse management systems (WMS). It is a feature that allows users to group and assemble individual items or components into a single kit or package. This module provides users with the ability to create a kit, track inventory of both kits and individual components, and manage the assembly of kits. It also enables users to specify the components and quantities needed for the kit.
The kitting module is an advantageous tool that offers greater efficiency and accuracy in managing inventory and assembly processes. It accomplishes this by grouping individual items into kits, making it easy for users to locate all the necessary components for a specific product or order. This feature saves time and effort that would otherwise be spent locating and gathering individual items, which is especially useful in high order volume or complex assembly environments. Additionally, the kitting module can help to reduce errors in assembly and inventory management by providing a clear, organised view of all the components needed for each kit or product.
Features | Descriptions |
---|---|
Master Data Setting |
1. Item Profile Setting (Enhancement) 2. Item Component Setting (Enhancement) |
Work Order Wizard |
1. Work Order Transaction – Work Order Wizard (New) The Work Order Wizard allows user to generate work order transaction with OPEN status by batch. The default number of batch will always be one if user does not specify any. There are two sections in this wizard requires user’s input. a. Warehouse Code [Linked from Warehouse Profile] b. Source Code [Linked from Source Profile] c. Document Date d. Party Code [Linked from Customer Profile e. Party Branch Code [Linked from Customer Branch] f. Reference No. a. Item code [Linked from Item Profile which has Item Component setting] b. UOM Code [Linked from Item Profile which has Item Component setting] c. Item Variant Code [Linked from Item Profile which has Item Component setting] d. Quantity: Order e. No. of Batch(s) (Default always be one) User can proceed by clicking [Generate] button to generate work order transaction directly or clicking the [Analyze] button to retrieve a summary report to analyze any item shortage. 2. Work Order Summary Report (New) A new report to show the summary of the total quantity needed for the item components and the total usable quantity from inventory balance. User can then request the approval from management for the replenishment due to item shortage. a. Warehouse Code [Linked from Warehouse Profile] b. Source Code [Linked from Source Profile] c. Document Date d. Document Date e. Party Code [Linked from Customer Profile] f. Party Branch Code [Linked from Customer Branch] g. Reference No. h. Status |
Work Order Module |
1. Work Order Transaction – Work Order Module The Work Order allows user to create a transaction for managing the kitting operation which includes finished goods and item components. This module separated to one header and three details which are finished goods, item components and apply of the item components. a. Line Number (Indicates batch] b. Status c. Process d. Item Code [Linked from Item Profile which has Item Component setting] e. UOM Code [Linked from Item Profile which has Item Component setting] f. Item Variant Code [Linked from Item Profile which has Item Component setting] f. Quantity a. Line Number (Indicates batch] b. Status c. Process d. Item Code [Linked from Item Profile which has Item Component setting] e. UOM Code [Linked from Item Profile which has Item Component setting] f. Item Variant Code [Linked from Item Profile which has Item Component setting] g. Quantity h. Quantity Applied i. Quantity Issued j. Quantity Received k. Item Type Code [Linked from Item Type] l. Pallet Type Code [Linked from Pallet Type] m. Production Date: From n. Production Date: To o. Expiry Date: From p. Expiry Date: To q. Lot No. r.Serial No. a. Document No. b. Document Date c. Pallet No. d. Bin Code e. Quantity f. Pallet Type Code g. Item Type Code h. Production Date i. Expiry Date j. Lot No. k. Serial No. User can click on the function [Auto Allocation] to allocate the usable quantity from inventory balance to the item components’ order quantity according to the input criteria respectively. System will automatically reduce the quantity applied to the maximum quantity that can build finished goods if one of the item components has shortage. 2. Generate Issue (Item Components) – Work Order Module (New) User can proceed to generate issue from header after done the allocation and posted the work order. If there is discrepancy between Order Quantity and Allocated Quantity, system will prompt a confirmation dialogue for user to decide whether append the shortage of the item component into new line or just ignore it. |
Issue Module |
1.Generate Receive (Finished Foods) – Issue Module (New) When system detects the selected issue is generated from work order module, user can click on the [Generate Receive] function to create Receive transaction with the relevant finished goods according to the item components quantity(s) that has been issued. |